A selección de equipos para proporcionar a máis alta calidade e produtividade nunha operación de soldadura vai máis aló da fonte de enerxía ou da pistola de soldadura; os consumibles tamén xogan un papel importante. Os consellos de contacto, en particular, poden marcar unha diferenza significativa entre executar un proceso eficiente e acumular tempo de inactividade para corrixir os problemas. A selección da punta de contacto adecuada para o traballo tamén pode afectar a rendibilidade da operación de soldadura.
As puntas de contacto son as encargadas de transferir a corrente de soldadura ao fío mentres pasa para crear o arco. De xeito óptimo, o fío debe pasar cunha resistencia mínima, mantendo o contacto eléctrico.
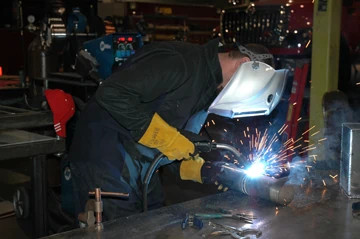
As suxestións de contacto poden marcar unha diferenza significativa entre executar un proceso de soldadura eficiente e acumular tempo de inactividade para corrixir os problemas, e tamén poden afectar a rendibilidade da operación de soldadura.
Por ese motivo, sempre é importante seleccionar un consello de contacto de alta calidade. Aínda que estes produtos poden custar un pouco máis que os produtos de menor calidade, hai un valor a longo prazo para negar ese prezo de compra inicial.
Ademais, as puntas de contacto de maior calidade adoitan mecanizarse con tolerancias mecánicas máis estreitas, creando unha mellor conexión térmica e eléctrica. Tamén poden presentar un orificio central máis suave, o que resulta en menos fricción a medida que o fío pasa. Isto significa unha alimentación consistente do fío con menos arrastre, o que elimina posibles problemas de calidade.
As puntas de contacto de maior calidade tamén poden axudar a minimizar as queimaduras (a formación dunha soldadura dentro da punta de contacto) e previr un arco errático causado por unha condutividade eléctrica inconsistente. Tamén tenden a durar máis tempo.
Selección do material adecuado e do tamaño da perforación
As puntas de contacto utilizadas para a soldadura MIG semiautomática adoitan estar compostas de cobre. Este material proporciona unha boa condutividade térmica e eléctrica para permitir unha transferencia de corrente consistente ao fío, á vez que é o suficientemente duradeiro como para soportar a calor xerada durante o proceso de soldadura. Para a soldadura robótica, algunhas empresas optan por usar puntas de contacto de cromo circonio máis resistentes, xa que son máis duras que as de cobre e soportan mellor o tempo de arco aumentado dunha aplicación automatizada.
Na maioría dos casos, usar unha punta de contacto que coincida co tamaño do fío leva aos mellores resultados. Non obstante, cando o fío é alimentado desde un tambor (por exemplo, aqueles de 500 libras ou máis) e/ou cando se usa un fío sólido, unha punta de contacto de tamaño inferior pode mellorar o rendemento da soldadura. Debido a que o fío dun tambor adoita ter menos fundición, aliméntase a través da punta de contacto con menos ou ningún contacto; ter un orificio máis pequeno exerce máis presión sobre o fío, creando unha maior condutividade eléctrica. Non obstante, o tamaño inferior dunha punta de contacto pode aumentar a fricción, o que provoca unha alimentación errática do fío e, potencialmente, unha queimadura.
Pola contra, usar unha punta de gran tamaño pode diminuír a transferencia de corrente e aumentar as temperaturas das puntas, o que tamén pode provocar a queima do cable. Cando teña dúbidas sobre a selección da punta de contacto do tamaño adecuado, consulte a un fabricante de consumibles ou distribuidor de soldadura de confianza.
Como mellor práctica, comprobe sempre a conexión entre a punta de contacto e o difusor de gas para asegurarse de que está segura. En consecuencia, unha conexión segura reduce a resistencia eléctrica que pode provocar un superenriquecido.
Comprender o recreo da punta de contacto
O receso da punta de contacto refírese á posición da punta de contacto dentro da boquilla e é un factor importante que inflúe na calidade, a produtividade e os custos da soldadura nunha operación de soldadura. Específicamente, o receso correcto da punta de contacto pode reducir a oportunidade de salpicaduras excesivas, porosidade e queimaduras ou deformacións en materiais máis finos. Tamén pode axudar a minimizar a calor radiante que pode causar fallos prematuros da punta de contacto.
O rebaixe da punta de contacto impacta directamente no pegado do fío, tamén chamado extensión do electrodo. Canto maior sexa o receso, maior será a tensión e maior será a tensión. En consecuencia, isto fai que o arco sexa lixeiramente menos estable. Por ese motivo, o mellor stickout de cable é xeralmente o máis curto permitido para a aplicación; proporciona un arco máis estable e unha mellor penetración de baixa tensión. As posicións típicas das puntas de contacto son receso de 1/4 de polgada, receso de 1/8 de polgada, enrasado e extensión de 1/8 de polgada. Consulte a Figura 1 para coñecer as aplicacións recomendadas para cada unha.
Recreo/Ampliación | Amperaxe | Salida de cable | Proceso | Notas |
1/4 polgadas. Recreo | > 200 | 1/2 - 3/4 in. | Pulverización, pulso de alta corrente | Gas mesturado rico en argón, cableado con núcleo metálico, transferencia por pulverización |
1/8 polgadas. Recreo | > 200 | 1/2 - 3/4 in. | Pulverización, pulso de alta corrente | Gas mesturado rico en argón, cableado con núcleo metálico, transferencia por pulverización |
Fluxar | < 200 | 1/4 - 1/2 polgada. | Pulso de corrente curta e baixa corrente | Baixas concentracións de argón ou 100 por cento de CO2 |
1/8 polgadas. Extensión | < 200 | 1/4 polgadas. | Pulso de corrente curta e baixa corrente | Articulacións de difícil acceso |
Prolongando a vida útil da punta de contacto
O fallo da punta de contacto pode deberse a unha serie de influencias, incluíndo queimaduras, desgaste mecánico e eléctrico, mala técnica do operador de soldadura (por exemplo, variacións no ángulo da pistola e a distancia entre a punta de contacto e o traballo [CTWD]) e a calor reflectante do material de base, que é común en xuntas de soldadura de acceso máis estreito ou áreas confinadas.
A calidade do fío utilizado tamén pode afectar a vida útil da punta de contacto. O fío de mala calidade adoita ter un reparto ou hélice indesexables que poden facer que se alimente de forma errática. Isto pode evitar que o fío e a punta de contacto se conecten correctamente a través do orificio, o que resulta en baixa condutividade e alta resistencia eléctrica. Estes problemas poden provocar un fallo prematuro da punta de contacto debido ao superenriquecido, así como a mala calidade do arco. Para prolongar a vida útil da punta de contacto, teña en conta o seguinte:
• Use os rolos de accionamento adecuados para garantir unha alimentación suave do fío.
• Aumente as velocidades de alimentación do fío e alargue o CTWD para minimizar as queimaduras.
• Seleccione as puntas de contacto cunha superficie lisa para evitar que o fío se enganche.
• Recorte o revestimento da pistola MIG á lonxitude correcta para que o fío pase correctamente.
• Temperaturas de funcionamento máis baixas, se é posible, para reducir o desgaste eléctrico.
• Use cables de alimentación máis curtos cando sexa posible para obter unha alimentación máis suave. Se son necesarios cables de alimentación máis longos, intente minimizar os bucles para evitar que se enrosquen.
Nalgúns casos, pode ser desexable converterse nunha pistola MIG refrixerada por auga para axudar a manter os consumibles front-end, incluída a punta de contacto, máis fríos e funcionando durante máis tempo.
As empresas tamén deberían considerar o seguimento do seu uso de puntas de contacto, observando o cambio excesivo e abordando en consecuencia algunhas das precaucións suxeridas. Abordar este tempo de inactividade máis cedo que tarde pode axudar moito ás empresas a reducir custos innecesarios para o inventario, ao mesmo tempo que mellorar a calidade e a produtividade.
Hora de publicación: Xaneiro-04-2023