A porosidade, descontinuidades tipo cavidade formadas polo atrapamento de gas durante a solidificación, é un defecto común pero engorroso na soldadura MIG e con varias causas.Pode aparecer en aplicacións semiautomáticas ou robóticas e require eliminación e reelaboración en ambos os casos, o que provoca un tempo de inactividade e un aumento dos custos.
A principal causa de porosidade na soldadura de aceiro é o nitróxeno (N2), que se involucra no grupo de soldadura.Cando a piscina líquida se arrefría, a solubilidade do N2 redúcese significativamente e o N2 sae do aceiro fundido, formando burbullas (poros).Na soldadura galvanizada/galvanneal, o zinc evaporado pode ser axitado na piscina de soldadura e, se non hai tempo suficiente para escapar antes de que a piscina solidifique, forma porosidade.Para a soldadura de aluminio, toda a porosidade é causada polo hidróxeno (H2), do mesmo xeito que o N2 funciona no aceiro.
A porosidade de soldadura pode aparecer externa ou internamente (moitas veces chamada porosidade subsuperficial).Tamén pode desenvolverse nun só punto da soldadura ou ao longo de toda a lonxitude, dando lugar a soldaduras débiles.
Saber identificar algunhas causas fundamentais da porosidade e como resolvelos rapidamente pode axudar a mellorar a calidade, a produtividade e o resultado final.
Pobre cobertura de gas protector
A mala cobertura de gas de protección é a causa máis común de porosidade da soldadura, xa que permite que os gases atmosféricos (N2 e H2) contaminen o baño de soldadura.A falta de cobertura adecuada pode ocorrer por varios motivos, entre os que se inclúen, entre outros, unha baixa taxa de fluxo de gas de protección, fugas na canle de gas ou demasiado fluxo de aire na cela de soldadura.As velocidades de viaxe demasiado rápidas tamén poden ser culpables.
Se un operador sospeita que un fluxo deficiente está a causar o problema, intente axustar o medidor de fluxo de gas para asegurarse de que a taxa é adecuada.Cando se utiliza un modo de transferencia de pulverización, por exemplo, un fluxo de 35 a 50 pés cúbicos por hora (cfh) debería ser suficiente.A soldadura a maiores amperaxes require un aumento do caudal, pero é importante non establecer a taxa demasiado alta.Isto pode producir turbulencias nalgúns deseños de armas que interrompen a cobertura de gas de protección.
É importante ter en conta que as armas deseñadas de forma diferente teñen diferentes características de fluxo de gas (ver dous exemplos a continuación).O "punto doce" do caudal de gas para o deseño superior é moito maior que o do deseño inferior.Isto é algo que un enxeñeiro de soldadura debe ter en conta ao configurar a célula de soldadura.
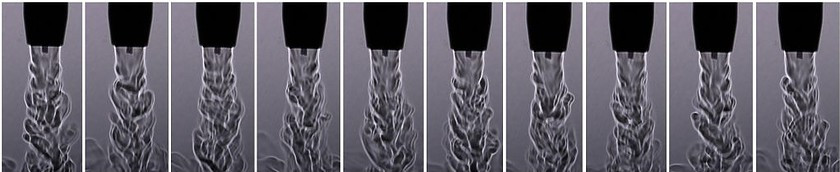
O deseño 1 mostra un fluxo de gas suave na saída da boquilla
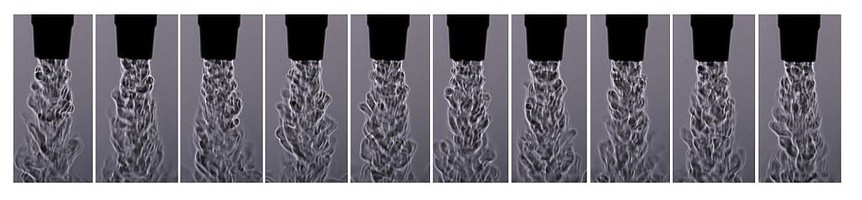
O deseño 2 mostra un fluxo de gas turbulento na saída da boquilla.
Comprobe tamén se hai danos na mangueira de gas, as conexións e os conectores, así como as juntas tóricas no pin de alimentación da pistola de soldadura MIG.Substitúeo segundo sexa necesario.
Cando use ventiladores para arrefriar os operadores ou pezas nunha célula de soldadura, teña coidado de que non apunten directamente á zona de soldadura onde poidan perturbar a cobertura de gas.Coloque unha pantalla na cela de soldadura para protexer do fluxo de aire externo.
Volve tocar o programa en aplicacións robóticas para asegurarte de que hai unha distancia adecuada entre a punta e o traballo, que normalmente é de ½ a 3/4 de polgada, dependendo da lonxitude desexada do arco.
Por último, baixa velocidades de desprazamento se a porosidade persiste ou consulta a un provedor de armas MIG para diferentes compoñentes front-end con mellor cobertura de gas.
Contaminación por metais base
A contaminación por metais base é outra razón pola que se produce a porosidade: desde aceite e graxa ata escamas e ferruxe.A humidade tamén pode favorecer esta discontinuidade, especialmente na soldadura de aluminio.Estes tipos de contaminantes normalmente conducen a porosidade externa que é visible para o operador.O aceiro galvanizado é máis propenso á porosidade do subsolo.
Para combater a porosidade externa, asegúrese de limpar a fondo o material base antes de soldar e considere usar un fío de soldadura con núcleo metálico.Este tipo de fío ten niveis máis altos de desoxidantes que o fío sólido, polo que é máis tolerante aos contaminantes restantes no material base.Almacene sempre estes e outros cables nunha zona seca e limpa de temperatura similar ou lixeiramente máis alta que a da planta.Facer isto axudará a minimizar a condensación que podería introducir humidade na piscina de soldadura e causar porosidade.Non garde os cables nun almacén frío nin ao aire libre.
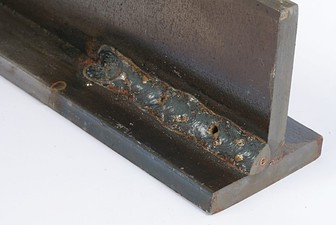
A porosidade, descontinuidades tipo cavidade formadas polo atrapamento de gas durante a solidificación, é un defecto común pero engorroso na soldadura MIG e con varias causas.
Ao soldar aceiro galvanizado, o cinc vaporízase a unha temperatura inferior á do fundido do aceiro, e as velocidades de desprazamento rápidas tenden a facer que a piscina de soldadura se conxele rapidamente.Isto pode atrapar o vapor de cinc no aceiro, dando lugar a porosidade.Combate esta situación controlando as velocidades de viaxe.De novo, considere un fío de núcleo metálico especialmente deseñado (fórmula de fluxo) que promove a fuga de vapor de cinc da piscina de soldadura.
Boquillas obstruídas e/ou de tamaño insuficiente
As boquillas obstruídas e/ou de tamaño insuficiente tamén poden causar porosidade.As salpicaduras de soldadura poden acumularse na boquilla e na superficie da punta de contacto e do difusor, provocando un fluxo de gas de protección restrinxido ou facendo que se volva turbulento.Ambas situacións deixan a piscina de soldadura cunha protección inadecuada.
Para agravar esta situación hai unha boquilla demasiado pequena para a aplicación e máis propensa a unha acumulación de salpicaduras maior e máis rápida.As boquillas máis pequenas poden proporcionar un mellor acceso ás articulacións, pero tamén obstruír o fluxo de gas debido á menor área de sección transversal permitida para o fluxo de gas.Teña sempre en conta a variable da punta de contacto á punta da boquilla (ou receso), xa que este pode ser outro factor que afecte o fluxo e a porosidade do gas de protección coa selección da boquilla.
Con isto en mente, asegúrese de que a boquilla sexa o suficientemente grande para a aplicación.Normalmente, as aplicacións con alta corrente de soldadura que usan cables de maior tamaño requiren unha boquilla con diámetros maiores.
En aplicacións de soldadura semiautomática, verifique periodicamente a salpicadura de soldadura na boquilla e retírela con alicates de soldador (alicates) ou substitúa a boquilla se é necesario.Durante esta inspección, confirme que a punta de contacto está en boa forma e que o difusor de gas ten portos de gas claros.Os operadores tamén poden usar composto antisalpicaduras, pero deben ter coidado de non mergullar a boquilla no composto demasiado ou durante moito tempo, xa que cantidades excesivas de composto poden contaminar o gas protector e danar o illamento da boquilla.
Nunha operación de soldadura robótica, inviste nunha estación de limpeza de boquillas ou escariador para combater a acumulación de salpicaduras.Este periférico limpa a boquilla e o difusor durante as pausas rutineiras na produción para que non afecte o tempo de ciclo.As estacións de limpeza de boquillas están destinadas a funcionar en conxunto cun pulverizador anti-salpicaduras, que aplica unha fina capa do composto aos compoñentes da fronte.Demasiado ou moi pouco líquido antisalpicaduras pode producir porosidade adicional.Engadir un chorro de aire a un proceso de limpeza da boquilla tamén pode axudar a eliminar salpicaduras soltas dos consumibles.
Manter a calidade e a produtividade
Ao ter coidado de supervisar o proceso de soldadura e coñecer as causas da porosidade, é relativamente sinxelo implementar solucións.Facelo pode axudar a garantir un maior tempo de arco, resultados de calidade e máis boas pezas que se moven pola produción.
Hora de publicación: 02-02-2020